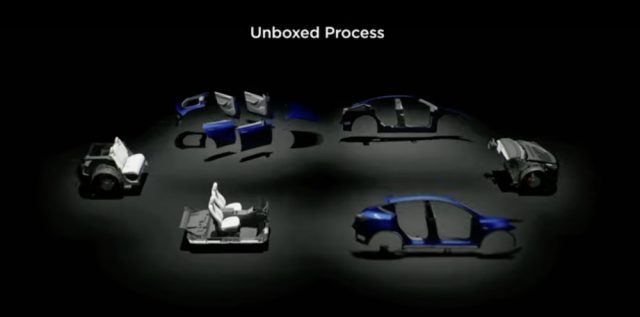
2023年3月、テスラがEVの新しい生産方法「Unboxed Process」を発表しました。これでEVの生産コストが半減する、と言っています。
2023年6月1日の日経産業新聞に詳しい解説記事がありますので、これを参考に見ていきましょう。
とてもひらたく言うと、Unboxed Processとは、車を6つのモジュールに分解し、各モジュールを組み立てて、最後に完成車を作るという方法です。
従来の車作りは、シャーシ(骨格)とボディ(車体)が一体化した車両構造(箱)を作り、そこに外板を取り付けていく、という流れ作業のプロセス。基本は100年以上前のT型フォードの生産方式と同じです。世界に名だたるトヨタ生産方式も、基本的にこの方法です。車の基本的な生産方式は、100年間変わりませんでした。
テスラのUnboxed Processは、名前の通り「箱」を作らずに、6つのサブラインで各モジュールを作り、最後にメインのラインで完成車を組み立てます。
この結果、作業性が向上します。たとえてみれば、ユニットバスのようなものです。マンションで風呂を作り込むのではなく、工場でバス設備一式を予め作っておき、マンションで組み立てて設置する感じです。
テスラはこれで大幅なコスト削減を狙っています。テスラは、現在の最廉価版EV「モデル3」と比べて半額のEVを作ろうとしています。そのためのコスト削減なわけですね。
一方で自動車の専門家は「コストはさほど下がらないのでは?」という意見。組立て工程コストは5割減らせますが、部品・材料を考えるとそれほどならないし、モジュール接続の材料で高くなる部分もある、と指摘します。
一方で工場の専門家は「組み合わせ型からモジュラー型に移行することで、コスト半減の可能性は十分ある」との意見です。実際、パソコンやデジタル家電はまさに同じ事が起こっていますね。
ちなみに7月の朝活永井塾のテーマ「学習する組織」で、経営学者ピーター・センゲはこんな事例を紹介しています。
米国自動車会社の重役が日本の自動車会社の工場を見学しました。 その重役は「本物の工場は見せてくれなかった」と不満顔です。在庫がなかったからです。
重役曰く、「私は製造業に30年携わってきたからわかる。在庫ゼロなんて視察用の芝居に決まっている」
その工場とは、在庫ゼロを実現したあのトヨタ生産方式の工場でした。「工場には在庫がある」と思い込む彼の目には、その後、米国自動車会社を圧倒した最新工場の真の姿が見えなかったのです。
業界への新規参入者は、ときに想像を超えた手を打ってきます。しかしその手は、業界で昔からやってきた人には非常識かもしれませんが、新規参入者にとっては当たり前の常識であることも多いのです。
テスラも、自動車業界の常識には囚われません。
たとえば今では多くの自動車メーカーが取り組んでいるソフトウェアでクルマの機能を追加するOTA (Over The Air)という技術も、もとはテスラが始めたものです。
長年自動車に関わってきた技術者は「クルマの機能追加は、カーディーラーで行うべき」と考えるのではないでしょうか? クルマの機能追加を無線ネットワークで更新するなんて発想は、なかなか難しかったでしょう。
しかしイーロン・マスクが熟知するIT業界では、ネットワーク経由での機能追加は常識。イーロン・マスクは、彼にとっての常識を自動車業界で行っているだけなのかも知れません。
これは新市場を開拓する際に、私たちも参考にすべき考え方だと思います。
自分たちが熟知する常識が、その新市場では非常識であれば、それは大きな武器になり得る、ということです。
テスラの挑戦は、私たちもぜひ参考にしたいものです。
■当コラムは、毎週メルマガでお届けしています。ご登録はこちらへ。